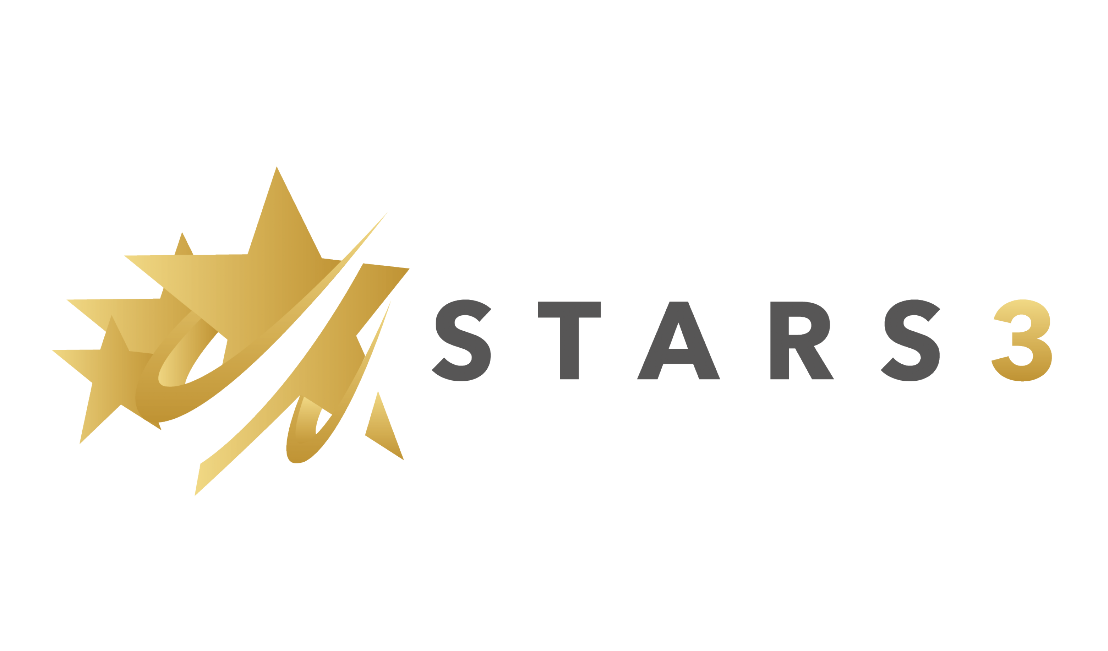
Chi siamo
Stars3 nasce dall'unione di tre professionisti con esperienza pluriennale, essa basa la propria strategia di sviluppo sulla produzione di utensili di alta qualità, sull'offerta di un servizio tecnico di assistenza al cliente qualificato e sempre attento alle specifiche esigenze produttive. La solida struttura tecnico-commerciale di Stars3 in sinergia con le unità produttive qualificano ulteriormente l'azione di Stars3 in favore di piccole e grandi aziende che vogliono migliorare i propri processi produttivi, testiamo nuovi prodotti e sviluppiamo nuove strategie di lavorazione per rendere gli utensili di Stars3 sempre più performante. Oggi, Stars3 si avvale di figure commerciali che operano sull'intero territorio nazionale ed estero; completa il ventaglio di attività una unità produttiva di costruzione di utensili principalmente attrezzata con affilatrici di alta precisione, per la realizzazione e affilatura di utensili che, per esigenze di mercato, richiedono un servizio al cliente più tempestivo. Nel corso del tempo il programma di utensili di Stars3 si è arricchito di numerose proposte che hanno configurato un’offerta veramente completa per quanto riguarda le frese standard e quelle chiamate speciali. La versatilità degli utensili di Stars3 favorisce la possibilità di esecuzione di profili specifici per le lavorazioni più complesse; si tratta, per esempio, di frese custom ed in generale di utensili che trovano applicazione nei moderni fresatori per la lavorazione di materiali quali: zirconio, fibra di vetro, polimeri,, compositi ceramici, cromo ed il titanio.
Stars3 offre soluzioni certe per la serenità di risultati sicuri

COME SCEGLIERE IL PROFILO DI UNA FRESA
Per profilo si intende la forma dell’estremità della
fresa atta al taglio, e normalmente può essere di tre tipi: cilindrico, torico
e sferico
- Profilo cilindrico: questi utensili hanno un’estremità piatta, presentano taglienti con angoli affilati disposti a formare un angolo di 90°
- Profilo torico: questo tipo di profilo smussato è utilizzato in sgrossatura, presenta un angolo affilato smussato da una forma raggiata. Questo arrotondamento aiuta a distribuire le forze di taglio in maniera più uniforme sull'angolo, contribuendo a prevenire l’usura, le scheggiature, prolungando così la vita dell’utensile.
- Profilo sferico: questo profilo è dato da utensili con taglienti che non hanno un’estremità piatta, ma raggiata, a creare un "tutto tondo" all'estremità della fresa
ERRORI COMUNI CHE SI COMMETTONO NELLA FRESATURA
- Velocità errata: eccessiva o troppo lenta Determinare velocità e avanzamento corretti per l’utensile e per le operazioni da eseguire, prima di avviare la macchina, è necessario. Bisogna comprendere quale sia la velocità ideale (RPM). Una velocità eccessiva può portare alla distruzione dell’utensile, al contrario, una velocità troppo bassa può provocare flessioni, una cattiva finitura, o semplicemente una asportazione di materiale troppo lenta. Se ci sono dubbi su quale sia la velocità ideale per la lavorazione che si intende eseguire, si può contattare il produttore dell’utensile
- Avanzamento errato: troppo o troppo poco L’avanzamento migliore per una lavorazione varia considerevolmente a seconda della tipologia di utensile e del materiale in lavorazione. Se l’avanzamento è troppo lento, si corre il rischio di tagliare nuovamente il truciolo, accelerando, di fatto, l’usura dell’utensile. Se invece l’avanzamento è troppo elevato, si potrebbe fratturare l’utensile
- Scelta del tipo di rivestimento Benché sia lievemente più caro, un utensile con un rivestimento ottimizzato per il tipo di materiale che intendiamo lavorare può fare una grande differenza. Molti rivestimenti aumentano la scivolosità (capacità di far scorrere il truciolo sul tagliente e sull'elica), rallentando la normale usura dell’utensile, altri invece aumentano la durezza e la resistenza all'abrasione. Tuttavia, non tutti i rivestimenti sono adatti a tutti i materiali, e la differenza appare più evidente se si comparano i materiali ferrosi a quelli non ferrosi
- Usare frese con taglienti troppo lunghi Se una lunga lunghezza di taglio è assolutamente necessaria per alcuni lavori, tuttavia riduce la rigidità e la forza dell’utensile. Come norma generale, la lunghezza di taglio (o altezza del tagliente) di un utensile dovrebbe essere lunga solamente quel tanto che basta per fare in modo che l’utensile mantenga quanto più rivestimento originale possibile. Più è alto il tagliente, più l’utensile diventa soggetto a flessione, che ne accorcia la vita e aumenta le possibilità di frattura
ANATOMIA DI UNA FRESA
Le frese possono presentare molte dimensioni diverse, presenti nella descrizione dell’utensile. È importante capire come ciascuna dimensione possa influire sulla scelta dell’utensile e come anche piccole variazioni possano fare la differenza quando l’utensile è in rotazione
COME SCIEGLIERE IL NUMERO DEI TAGLIENTI (Z) DI UNA FRESA
Tradizionalmente, le frese possono avere uno o più taglienti. La norma che va per la maggiore è di usare due taglienti per fresare alluminio e materiali morbidi come pmma e la zirconia, e 4 taglienti per fresare leghe più dure come cromo e titanio. Dal momento che l’alluminio e le leghe non ferrose sono normalmente più morbide dell’acciaio, la robustezza dell’utensile non è di vitale importanza, l’utensile può avanzare più rapidamente e garantire un’asportazione di materiale maggiore grazie alla maggior ampiezza dei 2 vani truciolo (la rimozione del materiale viene facilitata dall'ampia distanza che si trova tra i due taglienti). I materiali ferrosi sono invece normalmente molto più duri e per lavorarli c’è bisogno della forza di un nocciolo più grosso. L’avanzamento è più lento, e ciò provoca una dimensione minore del truciolo, che può essere evacuato attraverso lo spazio più ristretto presente tra i taglienti di un utensile con nocciolo più grosso. Ciò consente anche di inserire più taglienti sull'utensile, cosa che, a sua volta, aumenta la produttività. La chiave delle moderne tecniche di fresatura è trovare il giusto equilibrio. I taglienti, denominati anche con la lettera "Z", sono la parte di una fresa integrale più facile da riconoscere, sono la parte anatomica della fresa che le permette di asportare il materiale.
TRATTAMENTO DI SUERFICIE DELLE FRESE UTILIZZATE PER LA LAVORAZIONE DEL CROMO E DEL TITANIO
Il rivestimento impiegato da STARS3 è stato studiato appositamente per la lavorazione ad alta velocità e a secco (o con lubrificazione minima) di materiali duri. Questo rivestimento mantiene l’integrità del filo tagliente fino a temperature di 1200 °C. Una caratteristica del tutto particolare è la sua composizione: un rivestimento multistrato con un ultimo strato nano-composito di nano-cristalli di nitruro di silicio in una matrice cristallina di TiN. Questa matrice è stata appositamente progettata per proteggere il tagliente dal calore, dalla ossidazione e dalla abrasione. Il rivestimento utilizzato da STARS3 può essere usato con successo per lavorazioni ad alte velocità di materiali duri, quali acciaio e leghe ad alto contenuto di nichel e titanio, è particolarmente idoneo per frese il metallo duro in operazioni di sgrossatura e finitura che provochino elevate temperature nell'interfaccia truciolo/tagliente. Le velocità di taglio variano generalmente da 100 a 300 m/min. in funzione delle condizioni di lavoro e del tipo di materiale da lavorare
TRATTAMENTO DI SUPERFICIE DEGLI UTENSILI UTILIZZATI PER LA LAVORAZIONE DELLA ZIRCONIA, FIBRA DI VETRO E COMPOSITI CERAMICI
Il rivestimento utilizzato da Stars3 per questa tipologia di utensili è il diamante. Il diamante ha raggiunto dei risultati eccezionali grazie alla massima resistenza all'usura. Il processo prevede la deposizione di un gas contenente carbonio su un substrato riscaldato in presenza di un gas contenente idrogeno, gli atomi di carbonio presenti nel gas vengono ionizzati e accelerati verso il substrato, dove reagiscono con gli atomi di idrogeno per formare il diamante. Il diamante è il materiale più duro conosciuto sulla terra; diversi fattori sono cruciali per ottenere prestazioni ottimali nelle applicazioni di taglio:
- il metallo duro
- i disegni e la geometria degli utensili
- l'ingegneria dell’interfaccia che comporta un’elevata adesione del rivestimento.
- preparazione della superficie del bordo dell’utensile
Il processo di rivestimento adottato da Stars3 comporta un pre trattamento chimico, una preparazione al rivestimento ed infine una ispezione pre-consegna. Il processo di pre trattamento chimico è necessario per ottenere una buona adesione del rivestimento, ci sono due ragioni principali per il processo di pre trattamento:
- Irruvidimento della superficie dell’utensile
- Ancoraggio meccanico dello strato diamantato al substrato di base.
Le soluzioni di rivestimento adottate da Stars3 per le sfide odierne nella lavorazione di polveri compatte e sinterizzate porta all'utilizzo del diamante per le seguenti motivazioni:
- Massima resistenza all'usura grazie alla durezza superiore.
- Distribuzione omogenea dello spessore del rivestimento sugli utensili da taglio.
La combinazione di basso attrito ed elevata resistenza all'usura consente velocità di taglio elevate. I processi di rivestimento al diamante utilizzati da Stars3 consentono una elevatissima affidabilità degli utensili.
TRATTAMENTO DI SUERFICIE DEGLI UTENSILI UTILIZZATI PER LA LAVORAZIONE DEL PMMA E COMPOSITO
Il rivestimento impiegato da
Stars3 sugli utensile da taglio per la lavorazione dei materiali come:
Compositi, Pmma e Fibra di vetro prende il nome TA.C (Tetrahedral
Amorphous Carbon). Nasce dall'esigenza di
associare le proprietà di altissima durezza del carbonio nella sua forma simile
al diamante con il basso coefficiente di attrito, le alte velocità anche senza
lubrificazione e l’altissima resistenza all'usura.
Le proprietà del TA.C
impiegato da Stars3 può avere una durezza di circa 7000 Vickers ed uno spessore
da 1 a 3 micron.
PER INFORMAZIONI
Clicca qui